3D划痕仪作为材料表面力学性能分析的核心工具,其核心功能在于通过精密力学加载与三维形貌成像的协同作用,实现涂层附着力、表面硬度等参数的量化评估。本文从机械结构、信号采集与数据处理三方面解析其工作原理。
一、机械结构:多轴联动与模块化设计的协同
3D划痕仪采用高精度XYZ三轴运动平台,其中Z轴配备闭环控制加载系统,可实现恒定力、递增力或台阶增力加载模式。划痕头通过压电陶瓷驱动器提供亚纳米级位移精度,加载力范围覆盖1000mN至200N,满足从纳米涂层到宏观材料的测试需求。设备支持快速更换划痕头,包括微米级(MSt-50)、纳米级(Nst-1)和宏观级(HSt-200)三种规格,适配不同测试场景。
二、信号采集:多传感器融合与实时反馈
在划痕测试过程中,设备同步采集四类关键信号:
1.力学信号:通过高热稳定性电容式传感器测量加载力与摩擦力,分辨率达0.1mN;
2.声发射信号:声发射传感器捕捉材料脆性失效时的冲击振动,频率范围覆盖100kHz-1MHz;
3.电接触信号:接触电阻传感器量化涂层失效时的电阻变化,灵敏度≤1μΩ;
4.三维形貌信号:高分辨率3D形貌仪(如白光干涉仪或共聚焦显微镜)以亚纳米级精度记录划痕前后表面形貌变化。
三、数据处理:形貌重构与力学性能关联分析
采集的原始数据通过以下步骤处理:
1.三维重构:利用相位测量轮廓术(PMP)或飞行时间法(ToF),将形貌仪采集的条纹相位信息转换为三维点云数据,纵向分辨率可达0.01μm;
2.划痕特征提取:通过边缘检测算法识别划痕轮廓,计算宽度、深度、体积等参数;
3.力学性能关联:结合加载力-位移曲线与形貌数据,计算涂层附着力(临界负载LC1、LC2、LC3)、划痕硬度等指标;
4.失效模式分析:通过声发射信号的频谱特征与形貌损伤形态,判定材料失效模式(如脆性断裂、塑性变形)。
四、应用场景:从科研到工业的广泛覆盖
1.材料研发:评估陶瓷涂层、硬质合金的抗划伤性能;
2.质量控制:检测汽车漆面、光学镜片的耐磨性;
3.失效分析:解析航空发动机叶片的疲劳损伤机制。
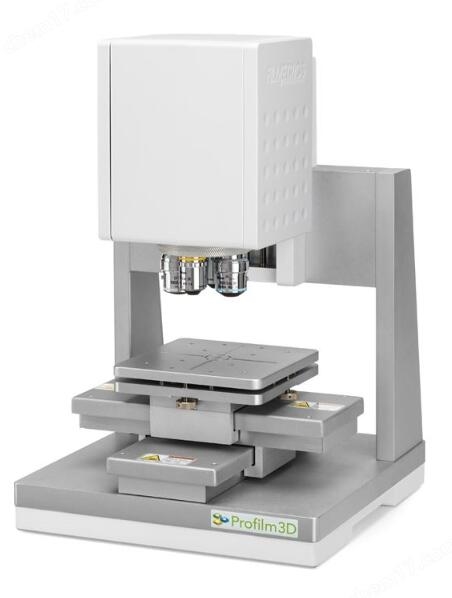
3D划痕仪通过力学加载与三维形貌成像的深度融合,实现了材料表面力学性能的精准评估。随着传感器技术与算法的持续升级,其在异常环境测试、多物理场耦合分析等领域的应用前景将进一步拓展。